DualPore™シリカで
微量物質の高効率吸着を実現
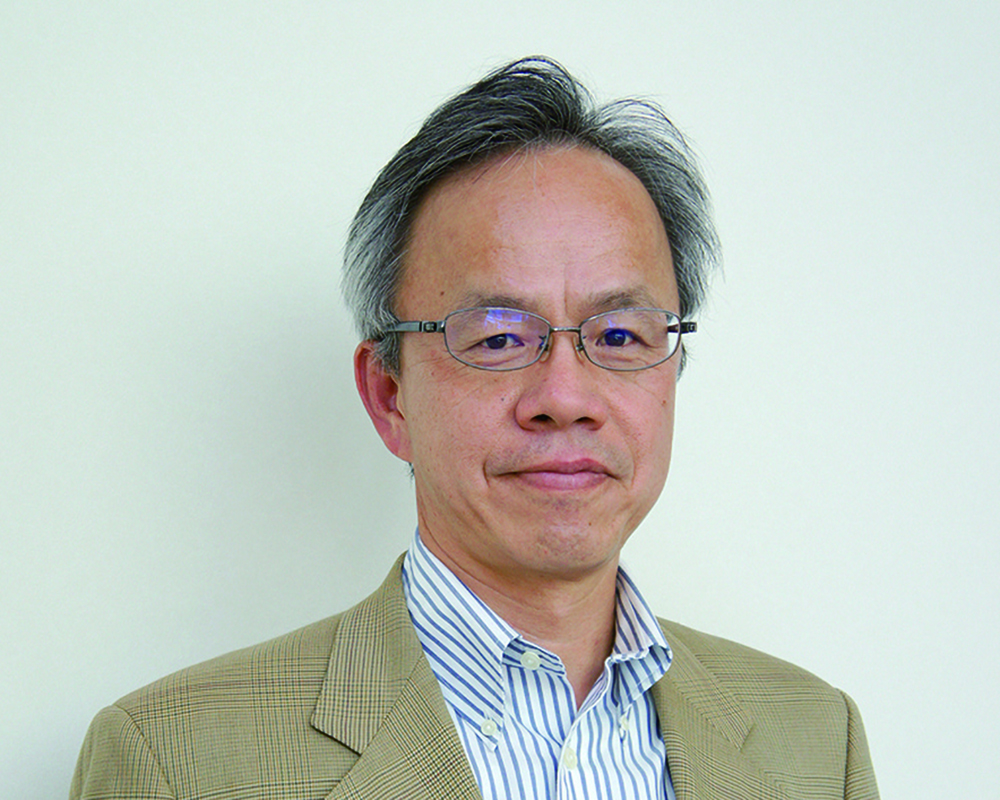
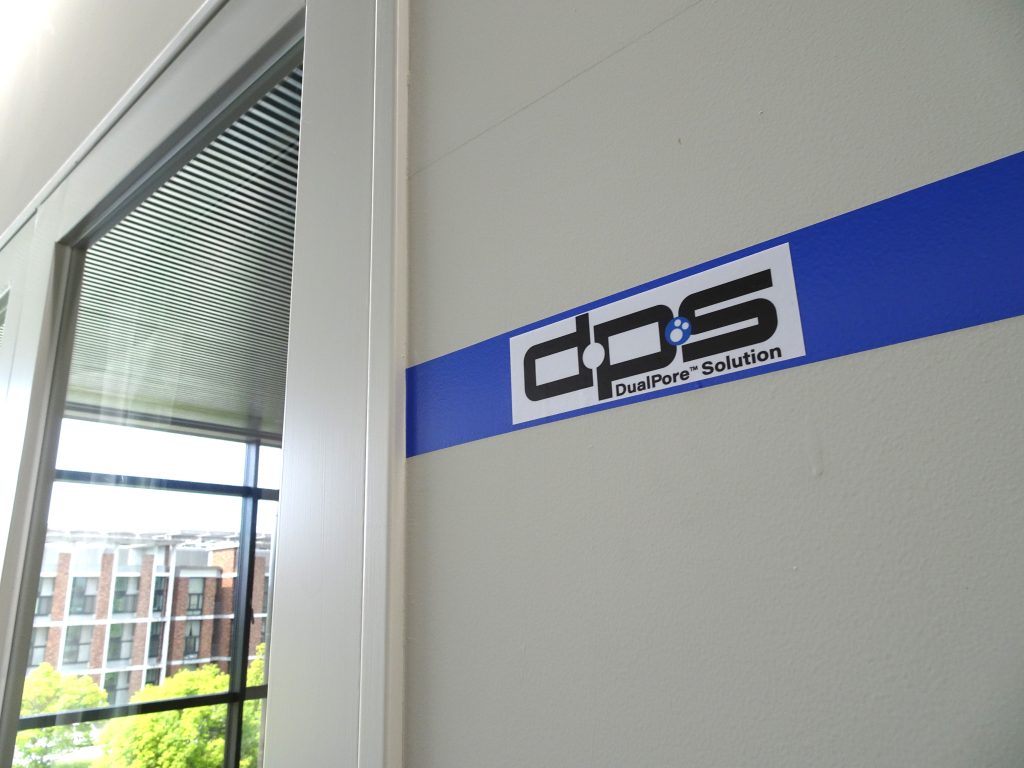
貴社の事業内容を教えてください。
ディーピーエスは、名古屋大学教授兼京都大学特任教授・中西和樹先生が30年前に発明した二段階の穴があるシリカ「DualPore™(デュアルポア)シリカ」の事業を行っています。発明当初から分析用のHPLCに用いるモノリスカラムとして大手化学メーカーから製品として実用化され、一世を風靡する技術と言われながら、その後なかなかそれ以上に進展しませんでした。ディーピーエスでは、このDualPore™シリカを吸着剤として汎用化させ、より効率性が求められる幅広い用途に展開しようとしています。
会社の設立経緯を教えてください。
ディーピーエスを設立したのは2017年の12月です。それまでの経緯として、まず2007年に設立されたREIメディカルという会社でシリカモノリスを使った透析医療用器具を発し、臨床試験を経てCEMarkも取得し技術開発としては成功したのですが、リーマンショックのためプロジェクトが販売段階で頓挫することになりました。しかしモノリスを作る技術は完成していたので、シリカモノリスのさらなる用途開発を行うため、2013年にエスエヌジーという会社を設立しました。このエスエヌジーでの活動の中で、モノリスではなくこれを粒状化した製品に特化した会社を別会社として設立してファイナンスする方が良いのではないかと考えて設立したのがディーピーエスです。 エスエヌジーでは、医薬精製用の分取カラムに数年取り組んでいました。しかし、作りこめば優れたものはできそうだったのですが、カラム一本数百万円するようなものになってしまい、それが何千本と販売できるような事業モデルはなかなか描けず、ファイナンスも難しいだろうと感じました。そこで、モノリスではなく粉にすれば、手間をかけて成形せずともカートリッジに詰めるだけで汎用的な吸着剤として使えるので、裾野を広げることができるのではないかと気づきました。投資家からファイナンスするにあたっては、そこの技術だけをまとめた方がお金を集めやすいだろうということで、ディーピーエスという会社を分けることにしたものです。現在ではエスエヌジーは休眠会社になっています。
白社長のご経歴と起業にいたった経緯をお聞かせください。
私はもともと大阪大学医学部の心臓外科医で、1990年代は心臓病に対する治療について、カテーテルから始まって、心臓移植再開や人工心臓などの研究を一生懸命やっていた時代でした。特にカテーテル治療というのが1980年代に始まって、アメリカでビッグビジネスになっていくのを見ていて、そういうことがなぜ日本でできないのだろうと思いました。医者として見ていると、医療のデバイスというのはほとんど輸入品なのですが、それらを作る技術は日本にあり、あるいは日本由来の技術であったりします。もっと独自の日本の技術を使って、それを応用できる製品はないのかという発想で、いわゆる用途開発を手掛けてみたいと、アメリカ留学を契機に思い立ったというのが大まかな経緯です。
大阪大学の心臓外科チームは、その後この教室を主宰した澤芳樹前教授が進める細胞シートなど日本発の最新の科学技術の研究を海外にも発信したいという思いの強いグループなのですが、なかなかそういった新しい材料というのは、たとえばiPS細胞が大きな可能性があることはわかっていても、それががん化するのではないかとか、そういった副作用が無いことを確認していくことも製品化には必須で、関門になってきます。これは化学材料でも同じことで、画期的な機能を持つ新材料も安全性などが問題になる。一方でディーピーエスが扱うシリカゲルというのは、もうすでに薬の充填剤などで使用されていて食べても安全であることは実証されているので、その特徴的な構造によって発揮できる機能性が活きる用途さえ編み出せば製品化できるよねと考えて、その用途開発・製品開発にチャレンジしたいなと思って、自分のライフワークとしてやり出したというのがきっかけです。
大阪大学大学院卒業後にスタンフォード大学に研究留学したのですが、スタンフォード大学というのはカテーテル治療を最初にやったところで、血栓除去バルーンカテーテルを発明した医者のFogarty博士のベンチャーキャピタルがあったりして、医療現場と新治療の開発が投資活動と一体となって行われているんです。そういうのを目の当たりにして、「あ、こういうようなことで、医療を進化させる役割を積極的にしている。しかも成功すればリターンを得られるという仕組みがあるんだ」と思いました。1995年に留学してそれを見て、「あ、こういうのは『いいビジネスの仕組み』だな」と、その時にようやく腹落ちしたんですね。そして、そういうことをやってみたいなとぼんやりと思いながら研究を続けつつ、医者に戻るのか、それとも次の人生としてベンチャーの世界に入るのかを考えていました。そしてMBAを取得し、アメリカの大手企業とベンチャー企業に勤めて40歳を超えたところで、日本でモノリス技術を利用して医療デバイスを作らないかと声を掛けていただき、REIメディカルに参画してこの技術に出会ったというのが流れです。
自分で起業する具体的なイメージは日本にいる時はなかなか描けませんでしたが、もともとの生い立ちが華僑の三代目で、貿易商の末裔であるという意識もずっとあって、医療でどういったことがビジネスとして成立するのかということは考えていました。余談ですが、父はすごく真面目な人で、「医療で金儲けをするな。大志を持った仕事をしろ」と言われていて、そういった父の教えがこの年齢になって改めて自分の中にはあったのかなと感じますね。
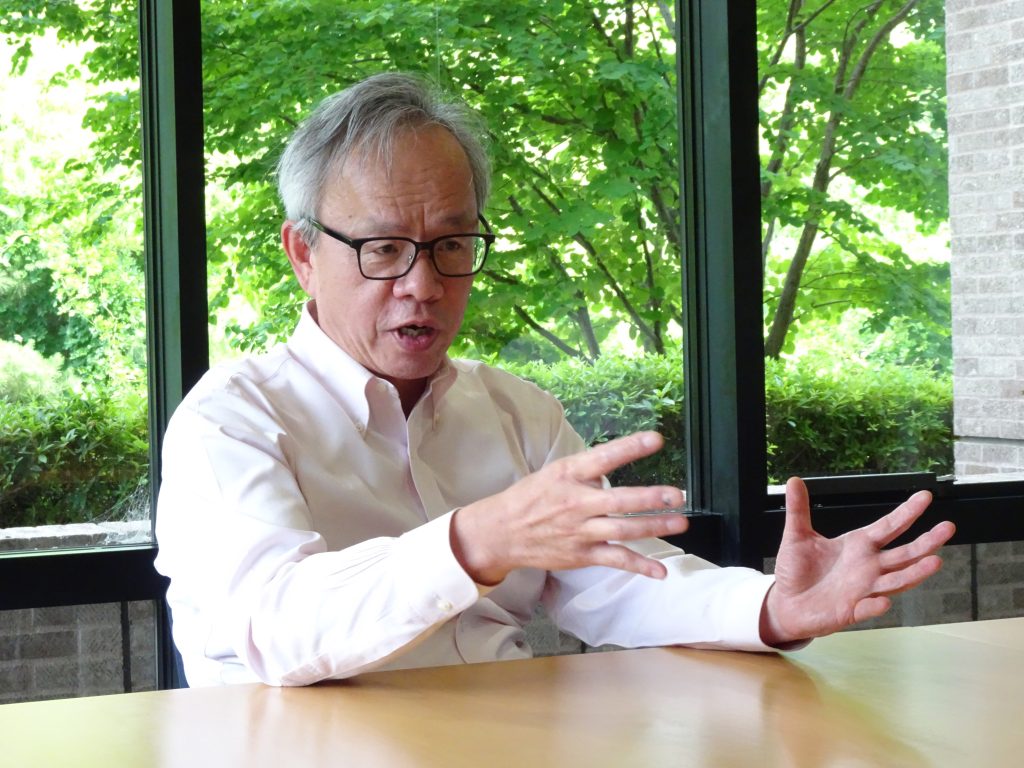
事業の基盤となる技術はどのようなものでしょうか?
ディーピーエスでは、京都大学で発明された二段階の穴があるシリカゲルを作っています。従来のシリカゲルは、身近な例では吸湿剤として用いるなど多孔質体として広く一番使われているもので、自然のものでは珪藻土などがあり、多くの穴が開いていて大きな表面積を持っています。 ディーピーエスのシリカゲルは人工的に作っているものですが、従来のシリカゲルが一種類の穴構造であるのに対し、弊社の「DualPore™(デュアルポア)シリカ」は二段階の穴が精緻に開いているため液通りが良いので、有効な表面積が非常に高くなっています。表面積が高く、しかも幹線道路が空いているような状態なので、そこで色々な反応の場を作ることができるわけです。そうすると、化学合成の合成反応もそうですし、あるいは今は吸着に取り組んでいますけれども吸着反応なども非常に効率よく起きるようになります。
最初、エスエヌジーでは、シリカゲルをモノリスにした一体型の製品をやっていました。そうする方が性能は最も発揮するのですが、ただこれを製品化しようとすると容器など諸々を全てカスタムメイドしなければならないという難しさがありました。一方で、シリカゲルの粉にしてしまえば、粉を用いた製品というのは従来からいっぱいあるので、そうしたところにこれを持っていけば使えるのではないかと考えて、ディーピーエスではあえて粉砕化したということです。ディーピーエスの技術的な強みは、やはり作る技術です。製造技術というかノウハウがあり、それをさぼるとうまくできないんです。
どのような市場/アプリケーションをターゲットとされていくのでしょうか?
現在はパラジウムの回収をターゲットにしています。パラジウムは、電子機器の表には出てこないところで、下地の材料として結構広く使われています。めっき液中で使用されているパラジウム量を金額換算すると何百億円の市場があるのですが、微量でしか使われていないので、逆に回収されていないということがわかっています。だからそこに一つニッチ市場があると思っていますし、その次に他の金属でも可能性があるのではないかと考えています。パラジウムで取り組んでいると、そこからの気づきがあってお客様の方から「こういうものがあるんだけど取れませんか?」といったニーズをおうかがいしています。それが現在のディーピーエスが持っている製品でできる場合もありますし、新たな良い濃縮回収技術として処方することも考えなければいけない場合もあります。
大きな事業テーマとして、微量物質の回収というのは技術的に非常に難しいわけですね。一方で島津製作所の田中耕一博士が2002年にノーベル賞をとられた質量分析装置のおかげで、微量なものがいっぱい見えるようになってきていますよ。そうすると、見えるようになった微量なもの、次には制御しよう、つまり除去したいとか濃縮抽出したいというニーズも必然と出てくるはずで、そこをどうやって拾っていくかということも考えていきたいと思っています。

事業化に向けて現在どの程度まで進捗されているのでしょうか?
既に製品としては装置も出来上がっており、お客様の工場への導入が始まっています。さらに言えば、製品を売るのではなくて、新しい濃縮回収ソリューションの提供という事業モデルを考えています。サブスクリプションというわけではありませんが、装置によって回収できたものを有価物にすることでキャッシュバックしますというような、レベニューシェアモデルのビジネス体系に持っていこうと提案しています。そうすることによって、お客さんとしてはリスクフリーで、捨てているものから収入が得られます。商流として有価販売させていただくところも日本有数の精錬会社と契約しました。低濃度排液を高度に濃縮することで、ほとんど純金と同じような値段で買っていただけることがわかっています。導入状況としては、国内では数社、海外では二社に導入されています。例えば、あるお客様では、国内にマザー工場があるので、そこに働きかけに行きました。そこで吸着できることは分かったのですか生産量がそこまで多くないので、引き続き働きかけをしたところ、大きな生産拠点が海外にあるということで、去年コロナ禍が明け実証試験を行い、正式採用に進めているところです。
今後の事業展開に向けた展望についてお聞かせください。
当面は、現在採用された案件で稼いで黒字化することを目指しています。大手のお客さんの中で採用が進んで複数のラインに導入してもらうことを優先順位高く進める一方で、小口のお客さんで年間数十万円程度捨てているようなところも拾っていくようなことを両方やっているという段階です。一方で、さらに事業を広げていくためには営業や技術サポートなど幅広く人的リソースを充実させていく必要があり、当社事業ならびに技術に投資し協業いただける大手企業を求めています。
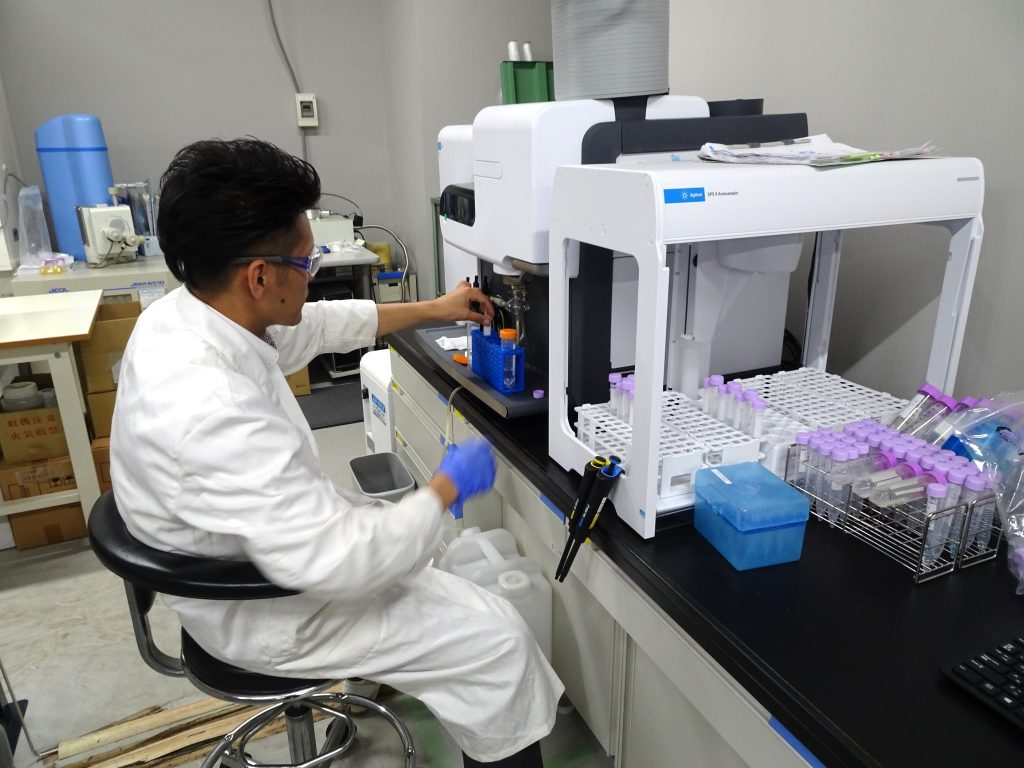
素材化学関連のメーカーや商社との協業に、どのようなことを期待されますか?
JETROでグローバルサウスといって比較的まとまった補助金事業が本年から出ていますが、特に資源関係などの日本の技術を海外展開するのにちょうどよい機会だと思っています。しかし、そういったお話ができる商社や現地のメーカーがなかなかいないなという感じです。だから支援事業が出ているのだと思いますが、商社というのはやはり情報あるいは商材繋ぎで、現場に対するアプローチができるところはあまりなさそうですし、リサイクル業者も廃材やロットアウトに対する買取の利ザヤビジネスのようで、エンジニアリングをかけようとすると負荷がかかりすぎてしまうようです。しかし、やはり技術導出するためには、その技術が先方にどうやってフィットするかというところが大事で、我々が必要としているのは技術サポートなんですよね。日本の技術に関して言えば、海外で売りたいわけですから、海外での技術サポートができないといけないわけで、そこができるところが少ないようです。
ウェビナーへの参加も含めて、日本材料技研(JMTC)とのコラボレーションについて、コメントがあればお願いします。
浦田社長のご経歴を先日お伺いし、日本材料技研を起業され取り組もうとされている課題について、ディーピーエスと似ているところがあるなと感じています。それをもっと精緻に、ファイナンスも含めて考えていらっしゃるなと思っています。そういった方に、私もあまり巡り合ったことがないので、色々と情報交換やアドバイスをいただけたらなと思います。また日本材料技研のネットワークから、事業提携やファイナンスなどにもご協力いただけたらありがたいなと思っています。
最後に、このインタビューページをご覧になる方に向けて、
メッセージをお願いします。
DualPore™シリカは従来とは無比な濃縮技術なので、使い方を一緒に考えて、事業化していただきたいです。「濃縮したら世の中変わるよね」というようなことを考えて一つ何かアイデアが出たら、アメリカ的に言えばそこがアプリケーションとしてテーマ設定できれば、一つのベンチャーになってしまうわけです。それを実証するために、パラジウムで証明しようと躍起になってやっていますが、本来はもうちょっと発想を変えた方がいいのかもしれません。私の元々の背景の医療分野に向ければ、サンプルを10倍濃縮できれば10倍の感度を上げられるはず、診断技術、ひいてはより効率的な治療に貢献できるアプリケーションやビジネスモデルが考えられると思っています。DualPore™シリカを要素技術として、いろんなアイデアを考えてもらえればと思います。
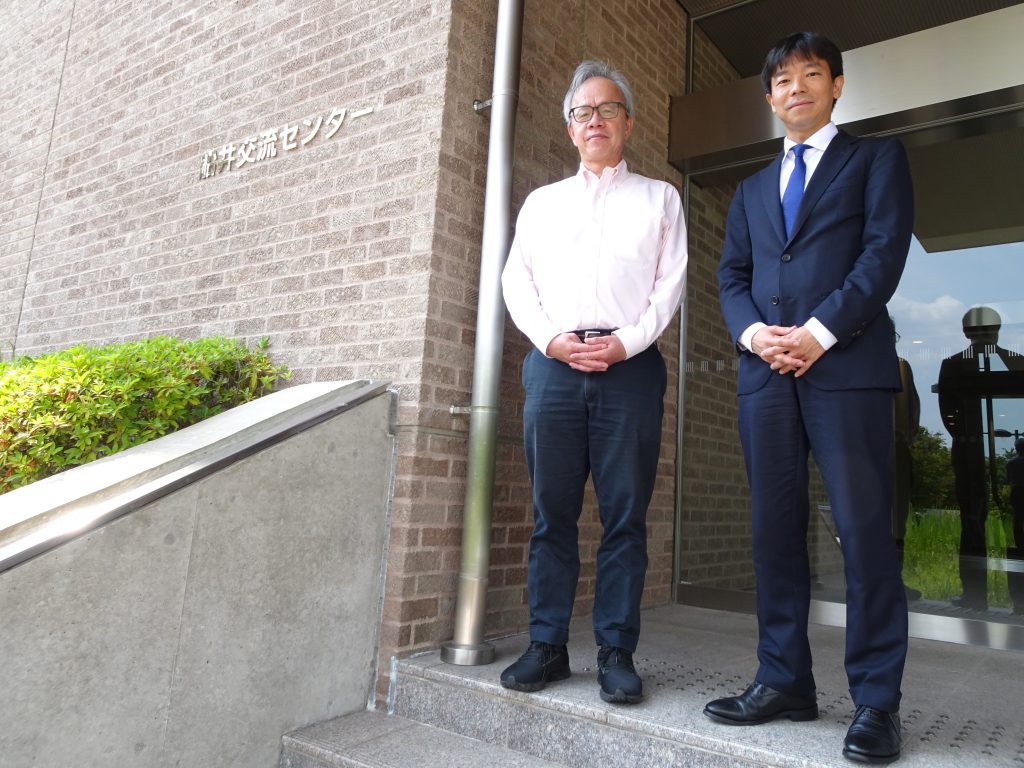
PROFILEプロフィール
COMPANY DATA企業情報
- 法人名
- 株式会社ディーピーエス
- 設立
- 2017年12月
- 本店所在地
- 京都府京都市
- 事業内容
- DualPore™粒子技術を応用した製品の製造・販売
- ウェブサイト
- https://www.dps-inc.co.jp/
-
振電相互作用密度理論により
機能性分子をピンポイント設計株式会社MOLFEX -
ソフトエレクトロニクス分野の
イノベーションハブとなるOPERA Solutions株式会社 -
モノの機能を自在に設計可能な
社会を実現するNature Architects株式会社 -
素材のプラットフォームを創出し
素材の流動性と循環性を最大化Sotas株式会社 -
世界をリードする単結晶技術で
新材料・新技術を迅速に社会実装株式会社C&A -
身の回りに溢れる未利用熱を
次世代のエネルギー源へ株式会社GCEインスティチュート -
藻類の研究開発で
人々と地球の未来に貢献する株式会社アルガルバイオ -
新規機能性可溶性ポリイミドで
次世代産業分野に貢献するウィンゴーテクノロジー株式会社 -
ヒトと農作物と環境に
優しい農薬を株式会社アグロデザイン・スタジオ -
多能性®中間膜で
世界をリノベートする株式会社Gaianixx